在半导体制造的封装测试环节,温度控制的精度与稳定性直接影响芯片的可靠性、性能及成品率。半导体深冷机(Chiller)作为核心温控设备,通过高精度、多场景的温控能力,为封装测试工艺提供了关键保障。
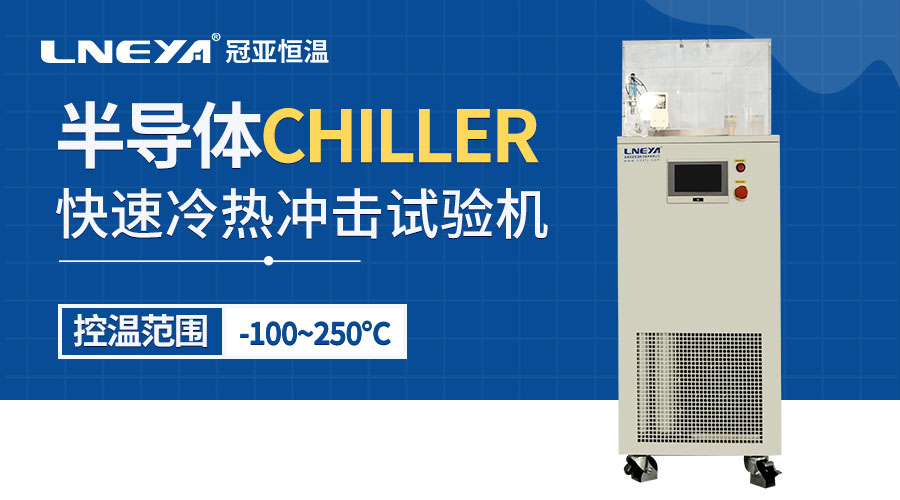
一、技术原理:高精度温控与动态响应能力
(一)帕尔帖效应与热电转换
半导体深冷机基于帕尔帖效应实现制冷,即当直流电通过N型和P型半导体组成的电偶对时,冷端吸收热量,热端释放热量。通过串联数十至数百对电偶形成热电堆,可实现-100℃至90℃的宽温域控制,温差电动势率(塞贝克系数)和电阻率是决定制冷效率的关键参数。
(二)动态控制系统与梯度控温
深冷机采用两组PID控制回路(主、从回路)结合前馈PV技术,实现温度梯度控制。例如,在芯片测试环节,设备可通过动态调整制冷功率,将测试环境温度波动控制在±0.1℃以内,避免因温度漂移导致测试数据失真。此外,全密闭循环管路设计配合呼吸孔,可延长导热油寿命并防止油雾结霜,确保系统长期稳定运行。
二、应用场景:覆盖封装测试全流程
(一)封装环节的温度控制需求
塑封工艺(Molding)
环氧树脂模塑过程中,模具温度需严格控制。深冷机通过高精度控温确保树脂固化均匀性,避免因温度波动导致元件翘曲或分层。
键合焊接(Die Bonding/Wire Bonding)
金线键合工艺中,键合头温度需在-10℃至+150℃间快速切换。深冷机通过液氮冷热冲击技术实现毫秒级响应,确保引线键合强度达标。
清洗与电镀(Cleaning/Plating)
晶圆清洗环节需控制清洗液温度以优化去污效果,电镀工艺则需维持镀液温度稳定以确保镀层均匀性。深冷机通过板式换热器与管道式加热器实现热交换,将温度波动控制在±0.5℃以内,使电镀层厚度均匀性提升。
(二)测试环节的温度保障需求
老化测试(Burn-in Test)
加速寿命试验中,多工位测试台需在-55℃至+175℃间循环。深冷机通过独立温控通道支持动态负载调节,使测试效率提升,同时降低因温度应力导致的早期失效风险。
终检(Final Inspection)
激光打标与电性能测试环节,深冷机为设备提供恒定环境温度(±0.2℃),确保测试数据可重复性。例如,某功率器件测试项目通过深冷机实现-40℃至+125℃宽域控温,产品直通率提高。
成品测试(Final Test, FT)
FT测试需模拟芯片实际工作场景,检测功耗、温度等参数。深冷机通过与测试机(Tester)和分选机(Handler)联动,为待测芯片提供稳定环境,避免因温度升高导致测试误差。
三、核心价值:提升良率、效率与可靠性
(一)保障产品性能一致性
半导体器件对温度敏感,微小波动可能导致电参数漂移。深冷机通过±0.1℃级精度控温,消除热应力对芯片的影响。
(二)提高生产效率与良率
缩短工艺周期
深冷机快速升降温能力(如从室温降至-40℃仅需5分钟)可缩短封装测试周期。
降低缺陷率
温度波动是导致焊点空洞、树脂分层等缺陷的主因之一。深冷机通过稳定控温,使封装缺陷率降低,显著提升良品率。
(三)支持先进工艺与材料
宽禁带半导体封装
碳化硅(SiC)、氮化镓(GaN)等材料对温度更敏感,需在-50℃至+200℃间准确控温。深冷机通过多级复叠制冷技术满足此类需求,推动半导体器件的可靠封装。
先进封装技术兼容性
先进封装工艺对温度均匀性要求高。深冷机通过分布式温控系统,确保晶圆级封装(WLP)过程中温度场一致性,支持2.5D/3D集成技术发展。
半导体深冷机通过高精度温控、动态响应能力及多场景适配性,针对不同封装测试场景,深冷机将提供从单通道(FLTZ变频系列)到多通道(无压缩机ETCU换热单元)的模块化解决方案,并支持非标定制,满足AI芯片、汽车电子等新兴领域的需求。